3 Interesting Facts About the Modular Building Industry
Marissa Morin | May 5, 2021
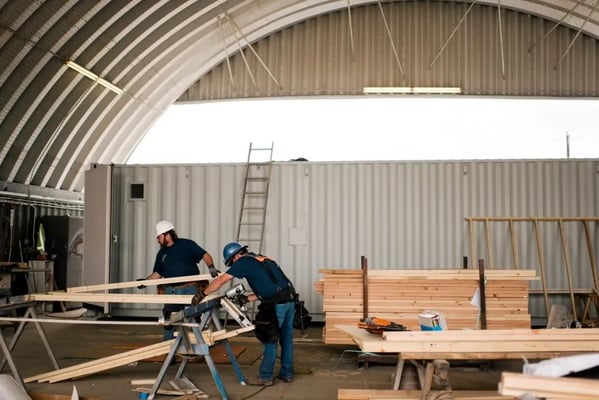
The construction industry – as a whole – indicates the nation’s economic health. When the construction industry is going well and growing, many other industries follow suit, and yet, despite the importance of the construction industry, it’s notorious for productivity problems. Construction has been tied to old technology, with strong resistance to innovation.
The modular building industry, a subsection of the larger construction industry, continues to grow in popularity thanks to its embrace of new technologies and refined processes. Modular construction offers new opportunities for construction by reducing project schedules, working with manufactured building elements, and promoting cost savings.
The Modular Building Industry Defined
McKinsey & Company defines modular construction as follows:
“In broad terms, modular construction involves producing standardized components of a structure in an off-site factory, then assembling them on-site. Terms such as ‘off-site construction,’ ‘prefabrication, and ‘modular construction’ are used interchangeably. These terms cover a range of different approaches and systems, from single elements that are clipped together using standard connections and interfaces to 3-D volumetric units with full fixtures.”
Let’s break it down further and look at three facts about the modular building industry. These three facts set modular construction apart and help create a future of new opportunities.
1.) Modular construction reduces projects schedules by as much as 50%
Reports of recent modular construction projects show that project timelines, when compared to traditional construction, accelerate by 20 to 50 percent. This statistic signals a drastic improvement for the construction industry, where many projects tend to run overschedule.
Why is modular construction faster? It’s due to the fact that work crews build both offsite and onsite simultaneously. The modular building industry utilizes manufacturing practices to create building elements in a factory-type setting. Work crews create building elements in a controlled setting, often regardless of the weather. While the manufacturing work takes place, a separate crew prepares the site for arrival and set up.
2.) Modular construction is broken into two categories – volumetric and non-volumetric
The modular building industry encompasses a variety of building elements, most easily understood when divided into volumetric and non-volumetric construction. In volumetric construction, three-dimensional units are created offsite and stacked together onsite. An example of volumetric modular construction is the use of modified shipping containers – our specialty here at Falcon. We modify each shipping container at our manufacturing facility, add windows, doors, insulation, air conditioning, and more – and then we ship them off for assembly at the prepared site. On the other hand, non-volumetric construction refers to the use of smaller prefabricated elements like wall panels, frames, and beams.
3.) Modular construction promotes cost savings
McKinsey & Company reports that “modular construction in European and US markets has the potential to deliver annual savings of up to $22 billion,” an industry-altering number. Much of these savings lie in the adoption of new technologies and innovation, such as the use of new and lighter-weight materials, as well as the improved precision and productivity thanks to manufacturing techniques. Keep in mind, that modular construction is not considered cheap, instead, it’s considered to be a more cost-efficient alternative when compared to traditional construction, for some projects more than others. The cost of modular construction per square foot is not significantly different from traditional construction, but the total project costs tend to be less, not to mention modular construction improves time to revenue with shorter project schedules.
The Modular Building Industry – Looking Ahead
The future of modular construction will likely evolve into even more advanced technologies as owners realize the efficiency, aesthetics, environmental impact, and strength of modular structures. The perception of flimsy and unattractive modular buildings is becoming a thing of the past. Now, buildings such as modified shipping container structures offer an eye-catching and impressively durable space for housing, offices, storage, and more. If you’d like to learn more about the possibilities of creating a modified shipping container modular building with Falcon, give us a call at 877-704-0177 or email us at Sales@FalconStructures.com.
SUBSCRIBE
- Shipping Container Modifications
- How-Tos
- Workspace
- Commercial Construction
- Multi-Container Buildings
- Storage Solutions
- Industrial Enclosures
- Oil & Gas
- Bathrooms & Locker Rooms
- Climate Control
- Green Building
- Living Space
- Industry Insight
- Military & Training Facilities
- Water Treatment Solutions
- Energy
THINK INSIDE THE BOX®
WITH OUR BLOG
Get everything from shipping container basics, to detailed how-tos and industry news in our weekly blog. Stay inspired and subscribe!
RELATED BLOGS
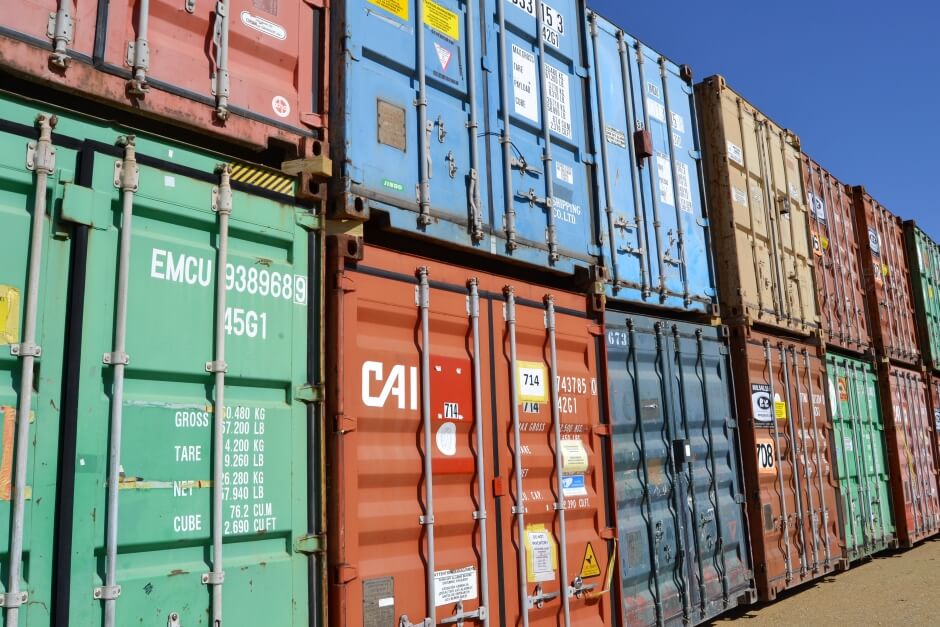
Could Shipping Containers Be a Solution to Affordable Teacher Housing?
Marissa Morin | Apr 19, 2023 | 3 min read
READ MORE
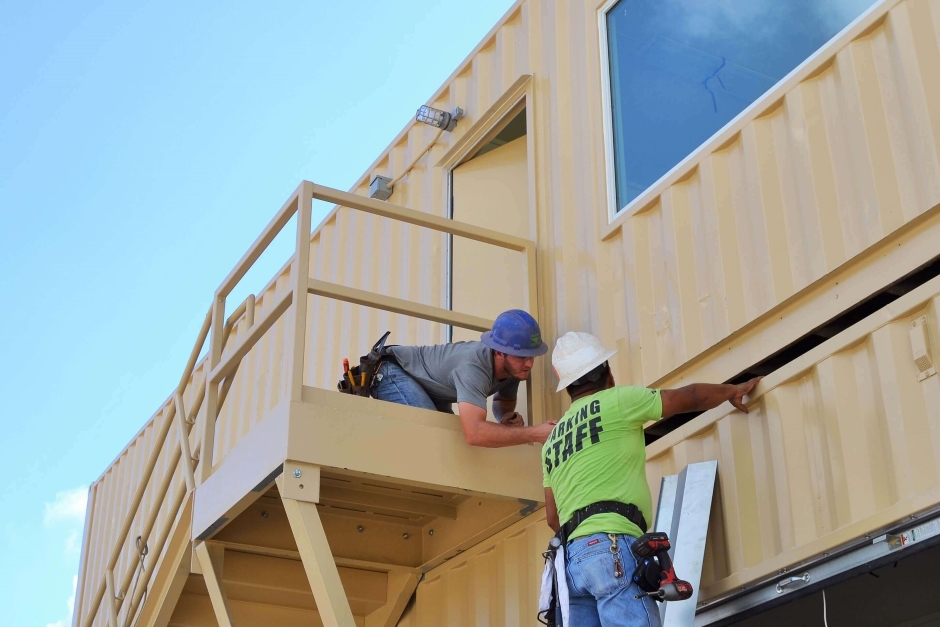
What Is Offsite Shipping Container Construction & Why Is It Important?
Marissa Morin | Apr 20, 2022 | 2 min read
READ MORE
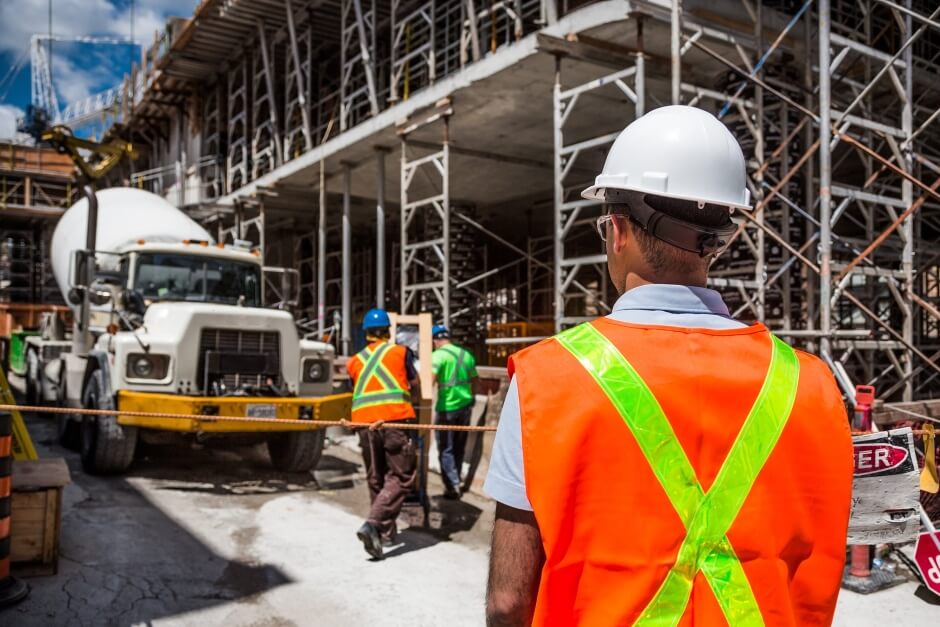
Modular vs Traditional Construction Cost: Which is Cheaper?
Marissa Morin | Jan 12, 2023 | 3 min read
READ MORE