Offsite Modular Construction
Every year, $10 trillion is spent on construction-related goods and services – making the global construction sector one of the largest in the world. An important subsection of the construction sector is known as offsite construction, or modular construction. To gain a better understanding of what offsite construction is, what the benefits are, and other helpful information, use this guide to aid your research – you’ll be a pro in no time!
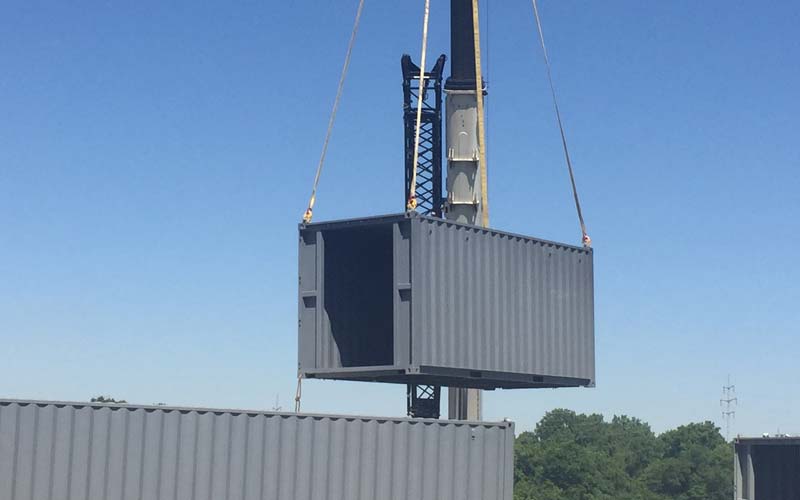
Offsite / Modular Construction
Modular construction is the process of building with prefabricated materials that are manufactured at a controlled, offsite location with the intention to later assemble the separate pieces onsite. This creates the opportunity to work on the building and the job site prep simultaneously, which reduces the overall completion schedule by as much as 50% when compared to traditional construction. Modular construction is broken up into two subcategories known as non-volumetric construction and volumetric construction.
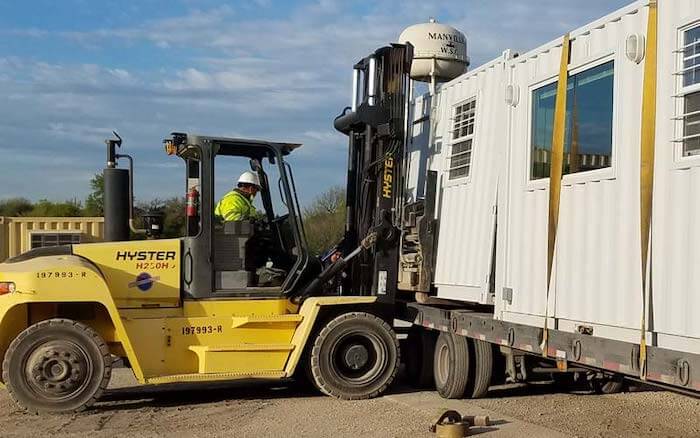
Volumetric Construction
Modular construction is the process of building with prefabricated materials that are manufactured at a controlled, offsite location with the intention to later assemble the separate pieces onsite. This creates the opportunity to work on the building and the job site prep simultaneously, which reduces the overall completion schedule by as much as 50% when compared to traditional construction. Modular construction is broken up into two subcategories known as non-volumetric construction and volumetric construction.
Permanent
Wood and Steel
Regardless of the type of construction project taking place, it’s likely that wood and steel will be utilized to complete the design. This often looks like three-dimensional boxes or elements built out of wood or steel that are made to be pieced together on site.
Modified Repurposed Shipping Containers
Similar to the box-like elements constructed using wood and steel, repurposed shipping containers can be modified into three-dimensional building elements to be stacked on top of one another or used as pieces within a structure.
Temporary (Relocatable)
Single Units
Single-unit structures are fairly common for temporary applications because they’re easy to move and often fill the purpose for a temporary living space or office. For structures that are intended to only stay in a single location temporarily or for those that will be frequently moved to different locations, single-unit models make relocation easy, thus are common solutions in these scenarios.
These structures are either trailers and purpose-built enclosures or modified and repurposed shipping containers.
Trailers are often used as temporary housing or office spaces, but shipping containers are growing in popularity as alternatives to mobile trailers.
They are about the same size and can be picked up by crane or forklift and easily loaded onto a truck to relocate.
Multi-Unit
Wood and Steel
Regardless of the type of construction project taking place, it’s likely that wood and steel will be utilized to complete the design. This often looks like three-dimensional boxes or elements built out of wood or steel that are made to be pieced together on site.
Multi-Unit
Repurposed Containers
Similar to the box-like elements constructed using wood and steel, repurposed shipping containers can be modified into three-dimensional building elements to be stacked on top of one another or used as pieces within a structure.
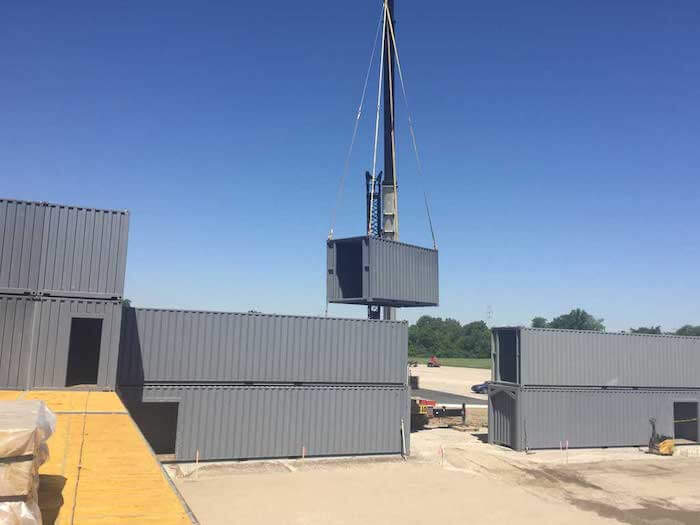
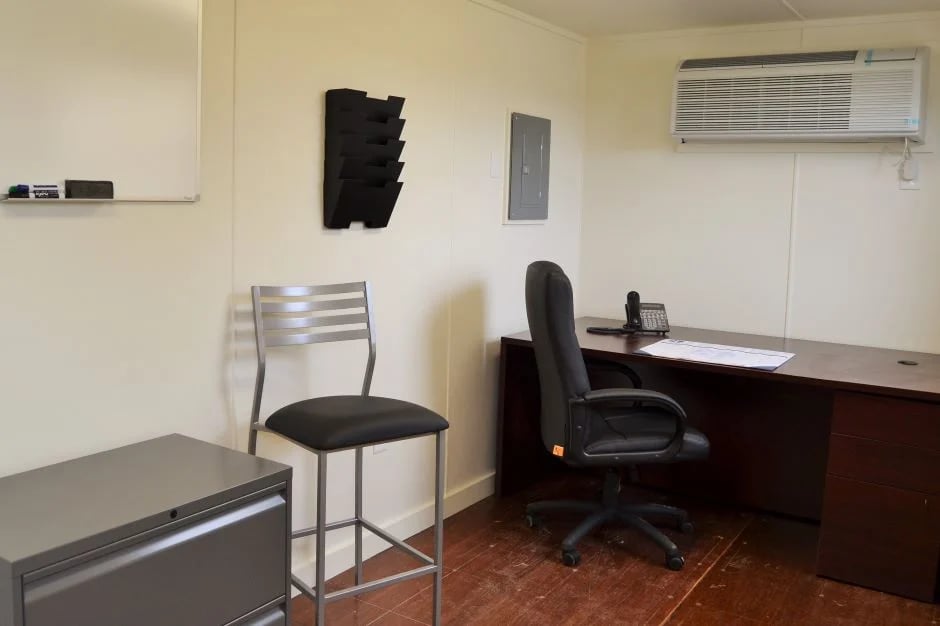
Where do Shipping Containers Fit In?
Modified repurposed shipping containers have become an increasingly more common element of modular construction. They are durable with heavy duty construction and easy to move around, making them ideal as basic building blocks of modular construction.
On top of their functionality, repurposing shipping containers as building elements is a practical way to implement green building. They’re three-dimensional blank canvases that can be modified as desired and easily transported, thanks to their initial creation as cargo boxes.
Non-Volumetric Construction
Building container-based structures off site just makes sense. We’re assembling buildings in 40% of the time traditional construction would take, and at a lower cost. I can very clearly see a future where container-based building is on the table for every structure.”
Benefits of Offsite Construction?
Offsite construction tends to produce more consistent quality through every stage in the production process. This is because offsite construction utilizes manufacturing techniques, building the same elements out of the same material uniformly.
The manufacturing environment typically employs systematic quality programs. It’s the uniformity of each piece created in a controlled environment that allows offsite construction to have more consistent quality, both throughout multiple stages in one project and across multiple projects.
Due to the consistent crew and the controlled workflow, offsite location projects tend to be completed on a shorter construction schedule. The controlled environment helps eliminate setbacks that put traditional construction projects behind schedule, such as bad weather days. Modular construction results in buildings opening 30% to 50% sooner than onsite construction.
According to the U.S. Labor Department Bureau of Labor Statistics, there are statistically less fatal injuries in manufacturing than in traditional onsite construction.
Although modular construction projects don’t always cost less than traditional construction, they often have a more predictable cost. The manufacturing environment oftentimes leads to less time wasted and less materials wasted, which reduces overall cost.
Since offsite construction removes the bulk of the physical project to a separate location away from the final site, work can be completed at both sites simultaneously. While the modules are being manufactured offsite, site prep can take place, saving a significant amount of time for the overall project.
Using manufacturing techniques such as implementing standardized measurements or elements for multiple projects helps to reduce material waste overall. A significant amount of the construction takes place in a controlled offsite location, therefore the scrap materials of one project can be used for another instead of discarded. Additionally, the final site of the project doesn’t have to be disturbed to the same extent as a traditionally built structure, helping to maintain the surrounding environment.
How Does the Modular Process Work?
The modular construction process is broken down into three early stages: pre-design, design, and post-design.
Stage 1: Pre-Design
Legality, financing, insurance, and project element ownership are established in the pre-design phase.
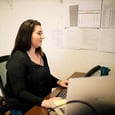
Stage 1
Stage 2: Design
The design phase includes correspondence between the architect and the modular manufacturer.
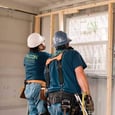
Stage 2
Stage 3: Post-Design
The post-design phase includes material procurement, and manufacturing team coordination as the project moves to the building phase. Then the teams work through the fabrication process, delivery, and assembly.
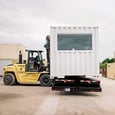
Stage 3
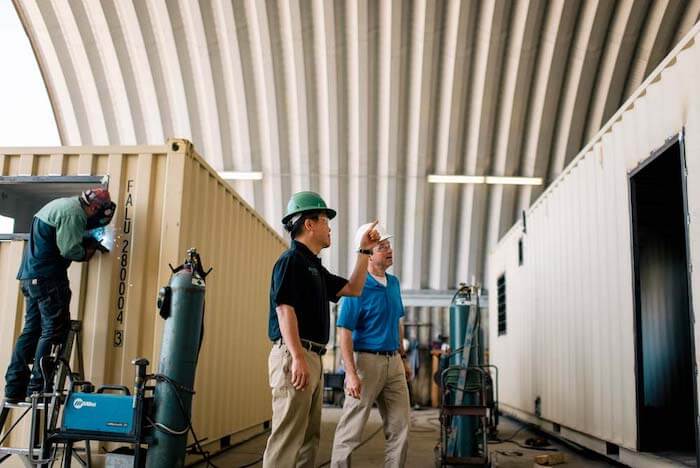
Modular Construction vs. Traditional
While offsite construction comes with the multiple benefits previously discussed, the offsite system of construction is not ideal for every project. It’s important to take into consideration the differences between the two systems and compare them against the type of project, the team that will build the project, and the location of the final site.
Modular Construction
In traditional construction, “large projects across asset classes typically take 20% longer to finish than scheduled and are up to 80 percent over budget” (McKinsey & Company).”
Pros
One of the most significant advantages of modular construction is that the overall project tends to be completed in significantly less time. This is primarily due to the controlled environment of the offsite facility that works with a consistent team. These teams have likely worked on similar projects before, making them familiar with the parameters of their assignment. They work to create a consistent quality of work and they tend to use materials more efficiently. Often the cost of the offsite process is more predictable, allowing companies to remain in budget and complete a project that closely resembles the referenced design plan. The same can hardly be said for traditional construction.
Cons
The downside of modular construction depends on the specifications of each project. For one, structural bulkiness can become an issue. If the modular elements are larger and nearer to final completion they can be challenging to transport; limits in transportation possibilities may restrict the size of the elements; spans and configurations of design may also be somewhat restricted; and the changeability of the physical structure can be made more difficult as the project advances. There is also less design flexibility in modular construction, meaning design changes should not be made in the building stages but should be avoided. Design decisions need to be made early to capture manufacturing efficiencies. In this case, design freezes need to be employed.
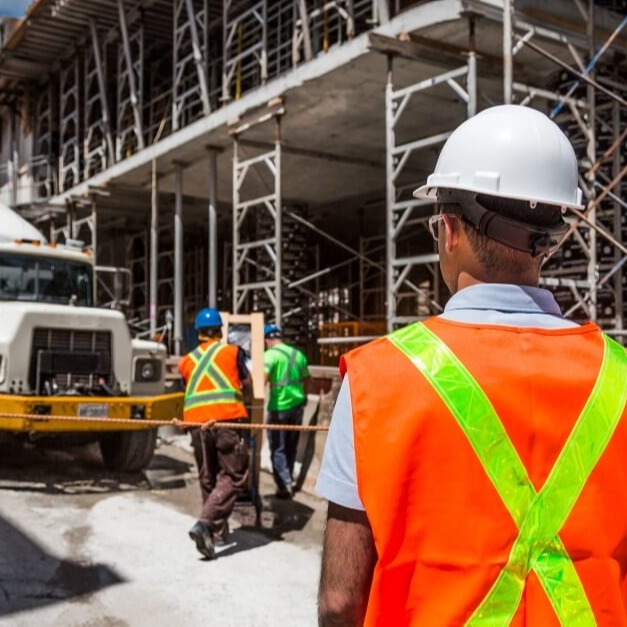
Is Offsite Construction Cheaper Than Traditional?
Although there is no promise that offsite construction is the cheaper option, savings between 15% and 50% have been commonly reported. These savings can be linked to the established manufacturer site, the quicker production process, and the ability for these controlled environments to avoid weather delays or subcontractor sequence delays that are unavoidable with traditional onsite construction.
Is Offsite Construction Cheaper Than Traditional?
Although there is no promise that offsite construction is the cheaper option, savings between 15% and 50% have been commonly reported. These savings can be linked to the established manufacturer site, the quicker production process, and the ability for these controlled environments to avoid weather delays or subcontractor sequence delays that are unavoidable with traditional onsite construction.
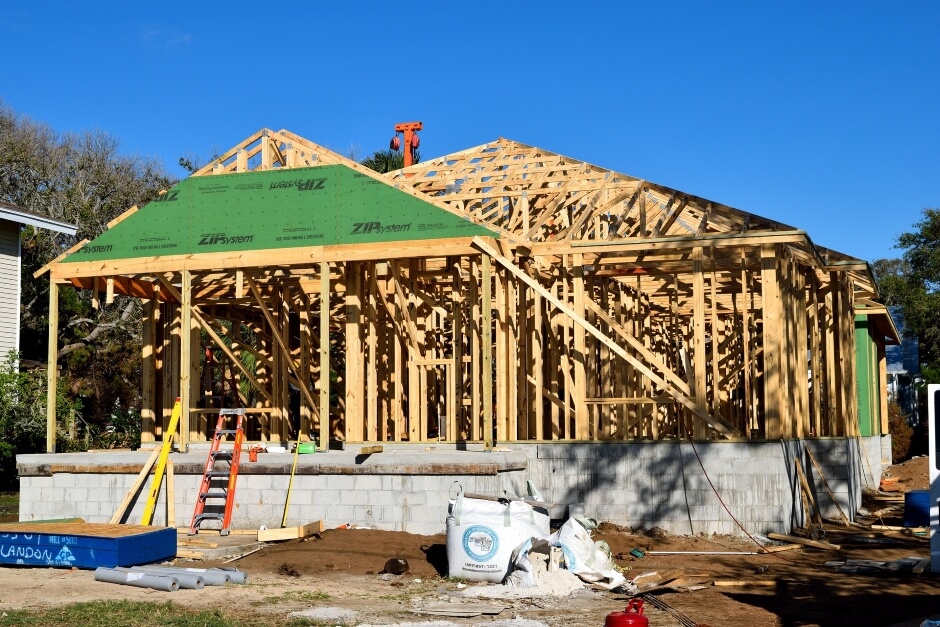
Is Offsite Construction Faster than Traditional?
In traditional construction, the structure can’t be built or worked on until the site has been prepared. Offsite construction allows both onsite preparation and offsite construction to happen simultaneously. During the time that offsite manufacturing and construction are taking place, the site can be prepared at the same time which drastically reduces the time of the overall project. Once the modules arrive onsite, assembly can begin immediately.
Is Offsite Construction Faster than Traditional?
In traditional construction, the structure can’t be built or worked on until the site has been prepared. Offsite construction allows both onsite preparation and offsite construction to happen simultaneously. During the time that offsite manufacturing and construction are taking place, the site can be prepared at the same time which drastically reduces the time of the overall project. Once the modules arrive onsite, assembly can begin immediately.
Modular Construction Statistics
The modular construction industry has seen substantial recent growth and is projected to grow more in the coming years. As of 2018, the industry was valued at USD 8.9 billion, according to the 2019 Permanent Modular Construction Report from the Modular Building Institute (MBI), and is projected to reach USD 157.19 billion by 2023.
The MBI has tracked the Permanent Modular Construction (PMC) market share value against the total construction market share in North America and they’ve noticed an increase in value from 2.38% in 2014 to 3.27% in 2017 and it continues to grow from there.
The modular construction market share has doubled over the last five years with many factories functioning at capacity. I expect the industry will continue to grow rapidly to meet increasing demand, pushing the boundaries of modular construction to new heights.” – Tom Hardiman, Executive Director of the Modular Building Institute.”
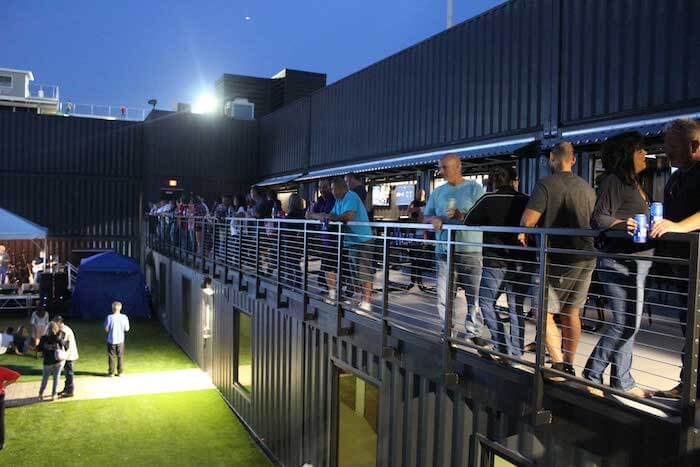
Common Modular Construction Projects
Permanent
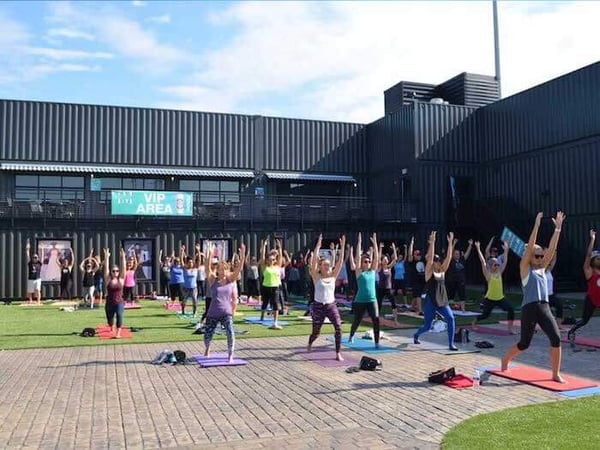
Modular Stadium Construction
An example of a modularly built stadium, made entirely from repurposed shipping containers, was completed by Falcon Structures using 122 container modules. Fortress Obetz located in Obetz, Ohio, is the largest shipping container building in the U.S. to date. Each container was prepared offsite at Falcon’s facility and shipped to its current location to be installed in a total of only 10 working days over a few months.
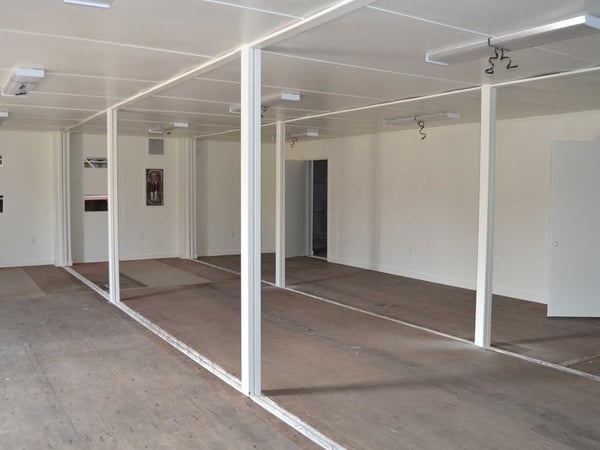
Commercial Modular Buildings
Many multi-level buildings, like apartments, are being built using modular construction. A current trend uses shipping containers that are modified individually offsite, then stacked together after delivery.
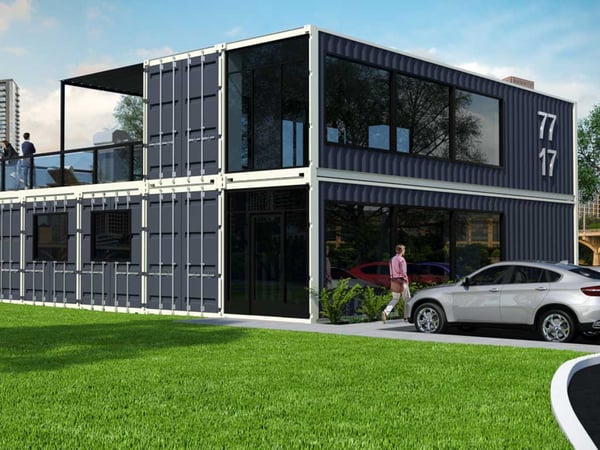
Modular Stadium Construction
An example of a modularly built stadium, made entirely from repurposed shipping containers, was completed by Falcon Structures using 122 container modules. Fortress Obetz located in Obetz, Ohio, is the largest shipping container building in the U.S. to date. Each container was prepared offsite at Falcon’s facility and shipped to its current location to be installed in a total of only 10 working days over a few months.
Relocatable
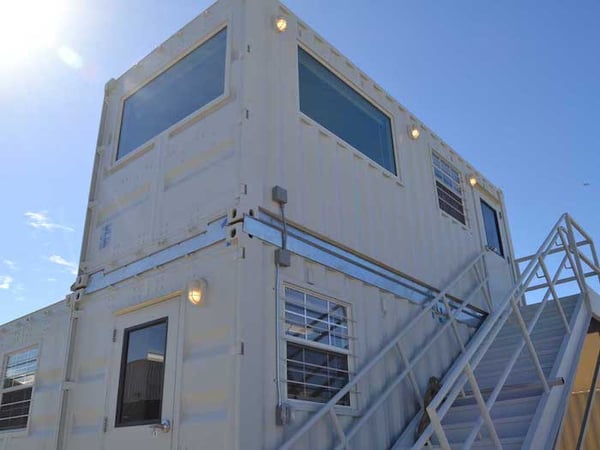
Modular Office Buildings
Office buildings built following modular construction practices can be either single-unit or multi-unit structures. These single-unit structures can be as small as a 10-foot shipping container or they can be as large as a multi-story building – which can, in fact, remain relocatable. Shipping container modular elements can be pulled apart, loaded onto a truck, and shipped to a new location with less hassle than moving a traditional building.

Government Modular Buildings
An example of a multi-unit living space was built by Falcon Structures for the Department of Homeland Security, which needed mobile workforce housing that could be relocated along the U.S. border. Not only did the structure need to be mobile, but it also needed to be secure, so repurposed shipping containers became the clear choice for this project.
Three 20-foot shipping containers were pieced together to make space for a bunkhouse for six workers and a restroom, kitchen, and living room. A custom chassis was built to hold the containers in anticipation of their frequent relocation.
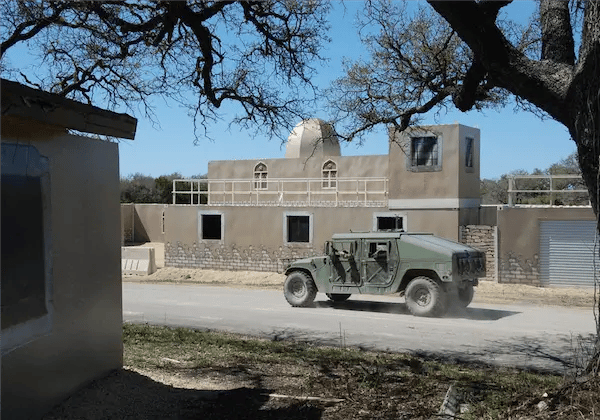
Military
Falcon Structures has built several military MOUT facilities (military operations in urban terrain) to help soldiers train for urban warfare. One of the MOUT structures included over 700 shipping containers. The use of shipping containers allows frequent reconfiguration of the facility, allowing the soldiers to train in environments that keep them on their toes.
Internally, the shipping containers were built out with moveable walls and doorways, and externally the containers were finished with a realistic façade resembling the cities they would be likely to see in combat.
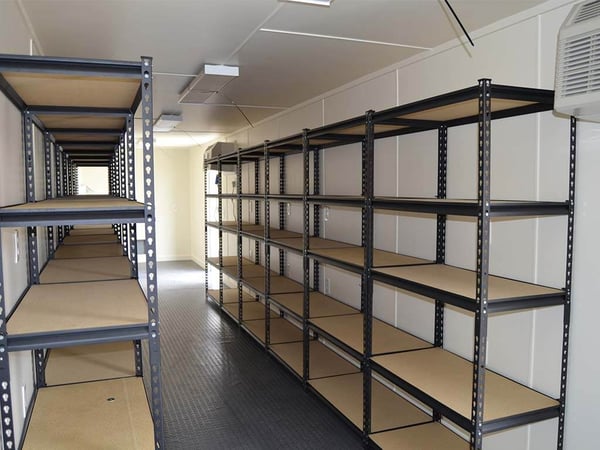
Storage
Single-unit storage structures are ideal when space is limited or where space does not exist, like in an open field. Shipping container storage units bring storage to a new level of security and accessibility.
The boxes can come in a variety of sizes, 10-foot, 20-foot, or 40-foot and they can be modified with a personnel door for easy access or the cargo doors can remain operable to make storing large items easier.
Need something beyond just a standard shipping container? Modify the unit with insulation, air conditioning, and internal and external lights to create exactly what you’re looking for.
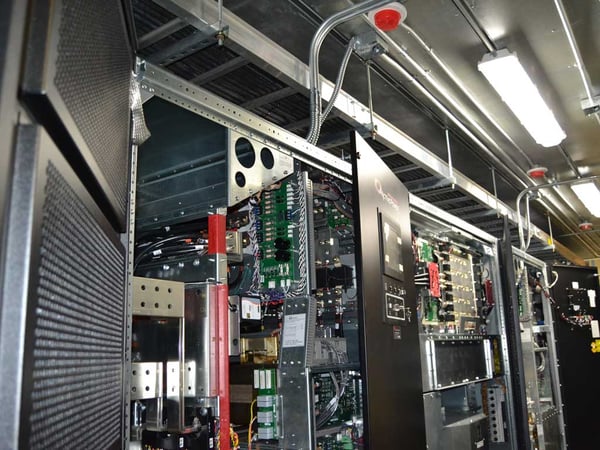
Equipment Enclosures
Repurposed shipping containers make great equipment enclosures for a variety of reasons. Most often, an equipment enclosure houses sensitive and valuable industrial equipment that needs to be kept cool and secure.
Examples of these types of enclosures range between server rooms, prefab uninterruptible power supplies (UPS) enclosures, audio equipment enclosures, remote terminal units (RTUs), and so many more.
These enclosures must be durable, portable, secure, and modifiable, so they can keep equipment safe in harsh climates, against thieves, or with frequent relocation. Additionally, many insulation and air conditioning options are available, which keeps equipment at the desired temperature.
Custom Shipping Container Buildings
It’s important when building with shipping containers that certain codes and regulations are met to ensure occupant safety, but one of the greatest benefits of shipping container structures is versatility. That versatility is created through thoughtful modifications.
Because shipping containers start out as open boxes, they can be cut, built out, and modified into the desired structure. Are you interested in learning more about custom modification possibilities? Check out shipping container modification options.
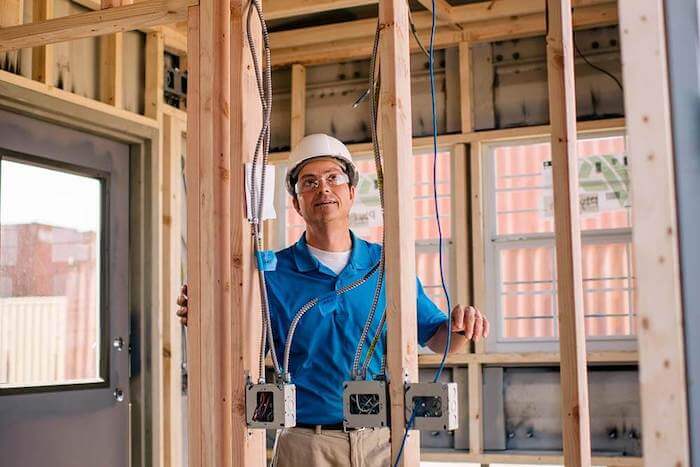
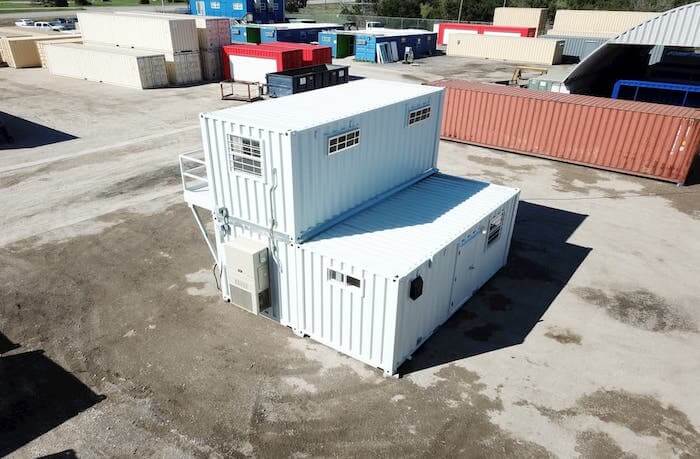
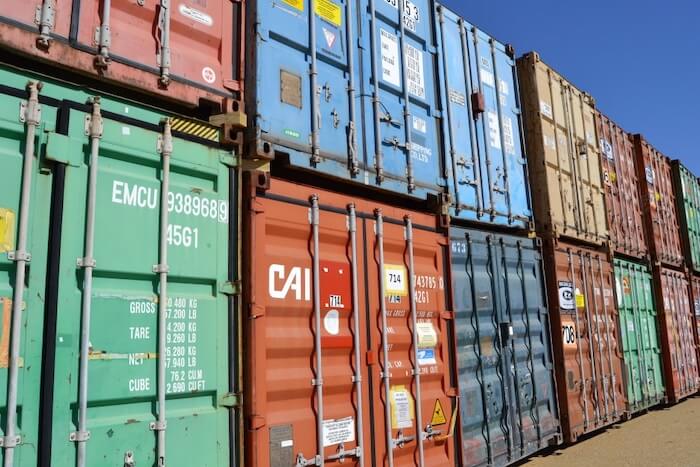
Design Considerations for Offsite Construction
Design considerations for offsite construction include a wide variety of possibilities. First, it’s important to think about the size of the structure. For shipping container modification, there are a few set sizes, yet some larger boxes can be cut down, combined, or stacked to create the desired configuration. From there, design considerations get more specific based on need. Will the structure be an office, a living space, a storage unit?
The answer to that question will then determine which door, windows, insulation, flooring, and so forth are the correct choice for that structure. To take a deeper look into offsite construction design considerations using repurposed shipping containers check out this free, downloadable eBook.
What’s Next for the Modular Construction Market?
The modular construction market is gaining momentum quickly, but it has likely just begun to take off. The obvious appeal to build quality structures, in less time and under controlled conditions, is a major pull. These projects often employ a consistent workforce, they tend to waste less material – or use repurposed material entirely, like shipping containers – and they don’t often suffer the setbacks that traditional construction projects are accustomed to.
With all of this being said, the future of the modular construction market is likely going to evolve and greatly expand in the near future. Here at Falcon Structures, we’re eager to see how shipping containers can continue to play a role in smart and safe offsite, modular construction.
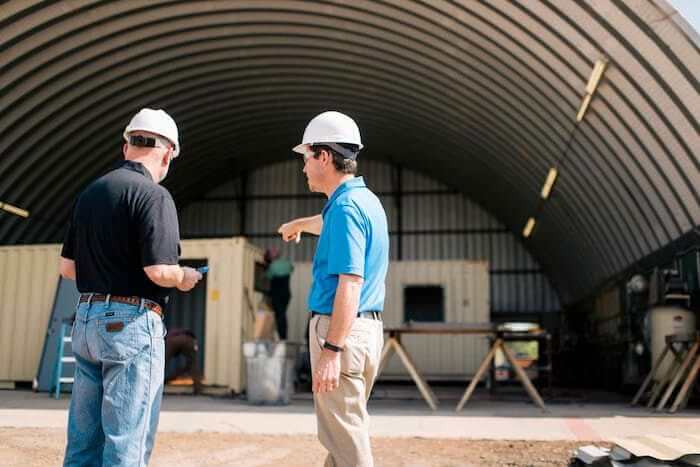
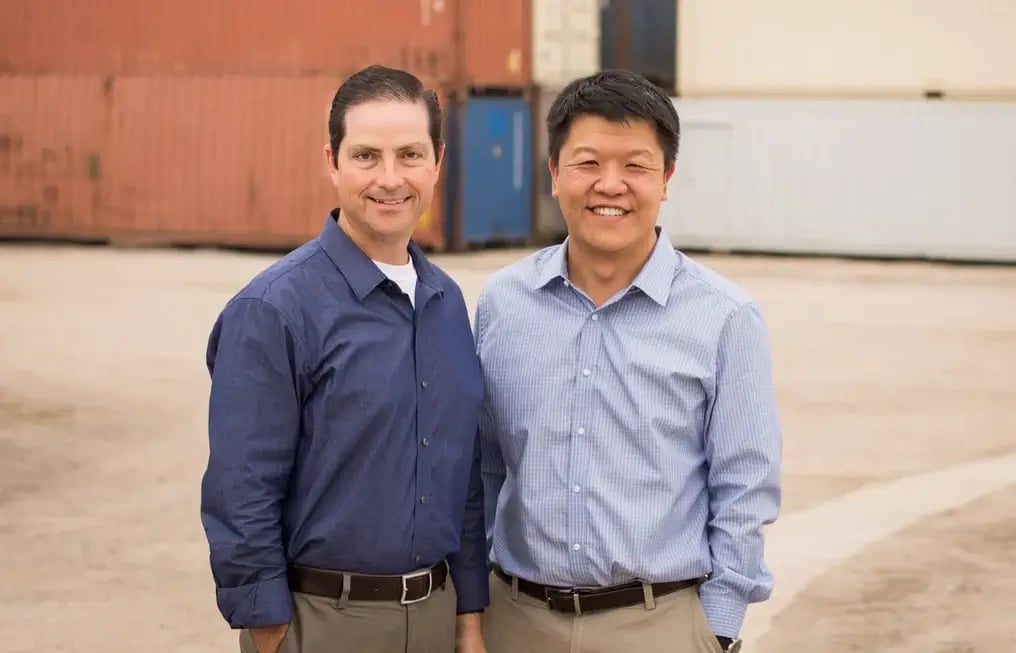
Want to discuss the benefits of modular construction for your next project?
Now that we know shipping containers are available, we’d absolutely use them for any outdoor or portable enclosure. It’s cost effective and robust. Falcon’s customizations made installation a smooth and easy process.”
BIG HOUSE SOUND