Top 4 Field Worker Challenges & How Employers Can Solve Them
Becca Hubert | Jan 8, 2025
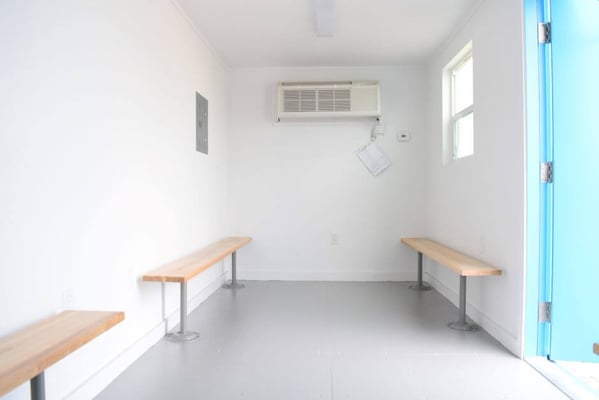
Field workers are the lifeblood of industries that drive our economy and sustain our way of life - construction, oil and gas, mining, and countless others. Their work is essential, demanding, and often takes place in remote and rugged environments. Yet, despite their indispensable role, they face challenges that seriously undermine not just their well-being, but also their productivity and job satisfaction.
Employers, let’s consider these challenges as more than operational hurdles. They’re opportunities.
By addressing pain points of field work, businesses can boost efficiency, reduce turnover, and prioritize the health and safety of their workforce. Plus, these efforts are likely to set companies apart as employers of choice.
1. Lack of Hygienic Facilities
The Challenge
The transient nature of field work is one of its greatest challenges, sending workers out where buildings and utilities may not exist. But basic human needs, like using the restroom and washing away grime or harmful residue, are mainstays no matter where a company sends its employees. It’s not uncommon for workers to endure unserviced porta potties or resort to nearby bushes for restroom breaks. In cases where workers are handling hazardous materials, a lack of proper facilities also makes it impossible to wash away harmful substances, increasing the risk of chemical burns, skin irritation, or long-term health issues.
Employers must also contend with facility needs for the increasing number of women in blue collar jobs, especially construction. That means accommodating them with female restrooms, but it also mandates private, clean spaces for pumping breastmilk if necessary.
What are the consequences of doing nothing?
- Workers “hold it” for unhealthy lengths of time
- Health risks if workers can’t wash away harmful debris, with potential OSHA intervention
- Potential legal action for failing to comply with regulations, such as the PUMP Act
- Employee turnover increases for any of the reasons above
Possible Solutions
- Install portable restrooms with handwashing stations
- Ensure regular facility cleaning and maintenance schedules
- Provide dedicated portable showers and clean spaces for workers handling hazardous materials
- Offer relocatable pump spaces for nursing employees
2. Lack of Climate-Controlled Break Facilities
The Challenge
Let’s consider a few common settings for field workers: A West Virginia mining operation during frigid winters. A remote construction site during a hot Texas summer. The far end of a tarmac during a lightning storm. Without proper shelter, field workers can be dangerously exposed to the elements.
What are the consequences of doing nothing?
- Employee overexposure resulting in heat stroke, hypothermia, dehydration, etc
- Injury from inclement weather like lightning strikes, falling tree limbs, flying debris
- Increased insurance premiums to account for workplace injury, or legal recourse
- Employees quit in droves because of dangerous and exposed working conditions
Possible Solutions
- Provide mobile, climate-controlled breakrooms that can travel from jobsite to jobsite as needed
- Equip structures with seating and hydration stations so workers can benefit from proper breaks
- Opt for sturdy structures that can withstand severe weather like rain and high winds to protect employees
Breakroom facilities that can be loaded and transported from site to site offer workers respite and shelter from the elements.
3. Long Commutes to Work
The Challenge
Field workers often face extensive commutes to their remote worksites, potentially (unpaid) hours both ways. This eats into workers’ personal time, but it also adds to stress and fatigue. It’s a common problem, especially within the oil and gas industry, where over 40% of work-related deaths are caused by motor vehicle crashes. The National Institute for Occupational Safety and Health (NIOSH) has created resources specifically for oil and gas companies and employees around this subject.
What are the consequences of doing nothing?
- Higher risk of accidents due to exhaustion
- Reduced productivity as workers start shifts fatigued
- Increased turnover as employees seek work closer to home
- Legal and insurance costs (NIOSH estimates the average cost to employers of an on-the-job fatal crash at $671,000)
Possible Solutions
- Provide accommodations near worksites for long-term projects. Examples include temporary housing or nearby rental units - something to minimize travel time
- Organize shuttles to safely transport workers to and from jobsites
- Schedule shifts so workers are allowed adequate periods of rest
4. Limited Access to Training, Safety, and Development
The Challenge
Field workers are often thrown into their role with minimal training or mentorship. This can leave them unprepared for the demands of handling specialized equipment, understanding safety protocols, or seeing any potential for career growth. With the absence of dedicated spaces for storing safety gear or conducting training sessions, field workers are far from set up for success in their work.
What are the consequences of doing nothing?
- Increased likelihood of on-the-job injuries and fatalities from insufficient training
- Higher legal and insurance costs from workplace accidents
- Elevated turnover as workers feel unsupported and unable to advance their careers
- Reduced overall efficiency and quality of work due to skill gaps and improper equipment usage
Possible Solutions
- Create on-the-job training and mentorship programs to provide hands-on learning opportunities
- Equip long-term jobsites with portable classrooms for safety workshops and skill development sessions
- Provide adequate storage for personal protective equipment (PPE) and ensure safety guidelines are clearly displayed
Portable classrooms are a growing solution for companies that prioritize jobsite safety training.
Employers: Why address these challenges?
By investing in solutions like hygienic facilities, climate-controlled shelters, transportation support, and increased safety measures, employers can reap the rewards of a safer, more productive and loyal workforce.
Your employees (and your bottom line) will thank you.
Want to stay up to date on ways to improve worker experiences in industrial settings? Subscribe to our biweekly Think Inside the Box newsletter on LinkedIn for industry insights, solutions, and use cases.
SUBSCRIBE
- Shipping Container Modifications
- How-Tos
- Workspace
- Commercial Construction
- Multi-Container Buildings
- Storage Solutions
- Industrial Enclosures
- Oil & Gas
- Bathrooms & Locker Rooms
- Climate Control
- Green Building
- Living Space
- Industry Insight
- Military & Training Facilities
- Water Treatment Solutions
- Energy
THINK INSIDE THE BOX®
WITH OUR BLOG
Get everything from shipping container basics, to detailed how-tos and industry news in our weekly blog. Stay inspired and subscribe!
RELATED BLOGS
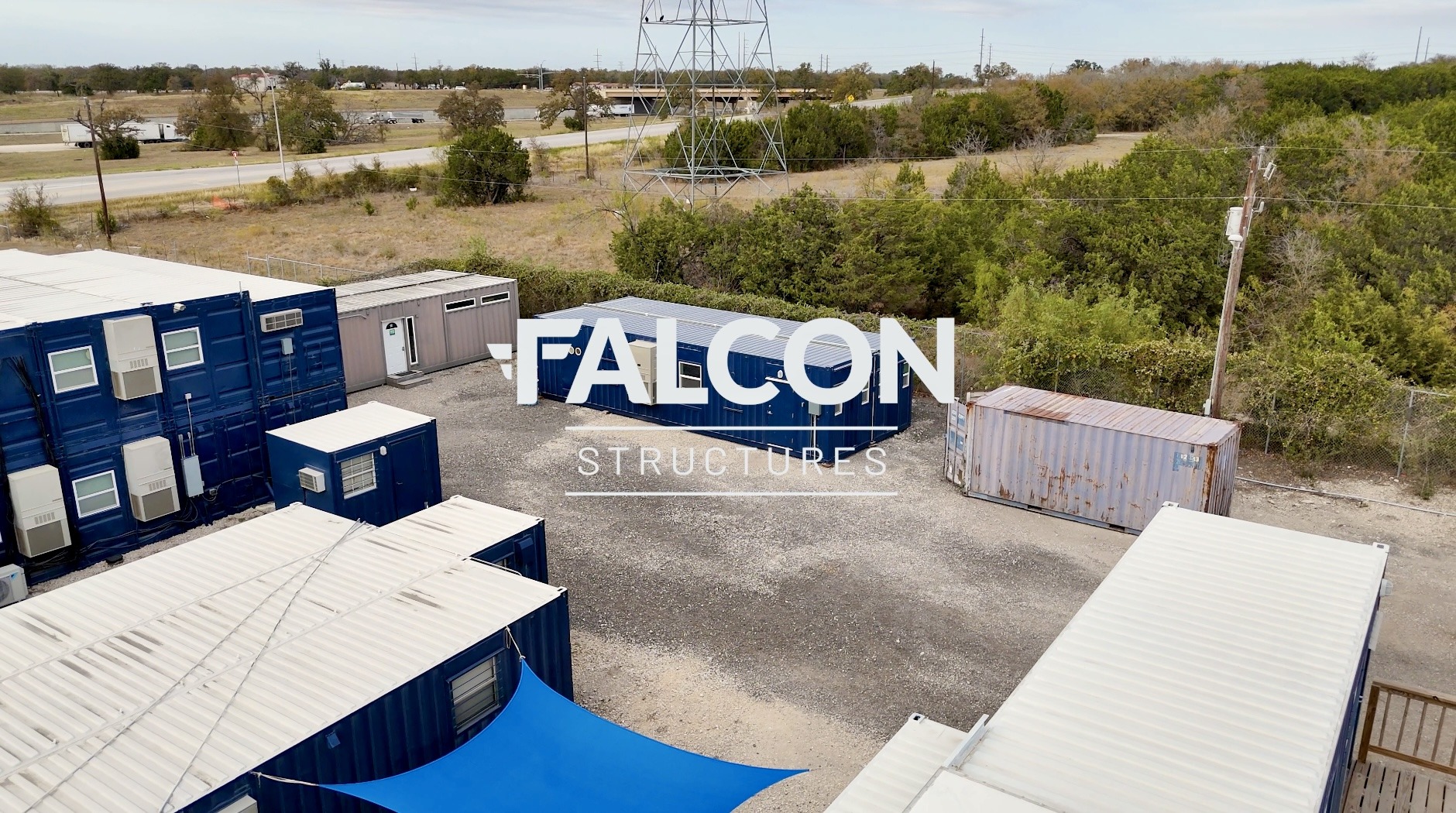
Building Better Workplaces: Behind Falcon's New Container Breakroom
Becca Hubert | Feb 5, 2025 | 4 min read
READ MORE
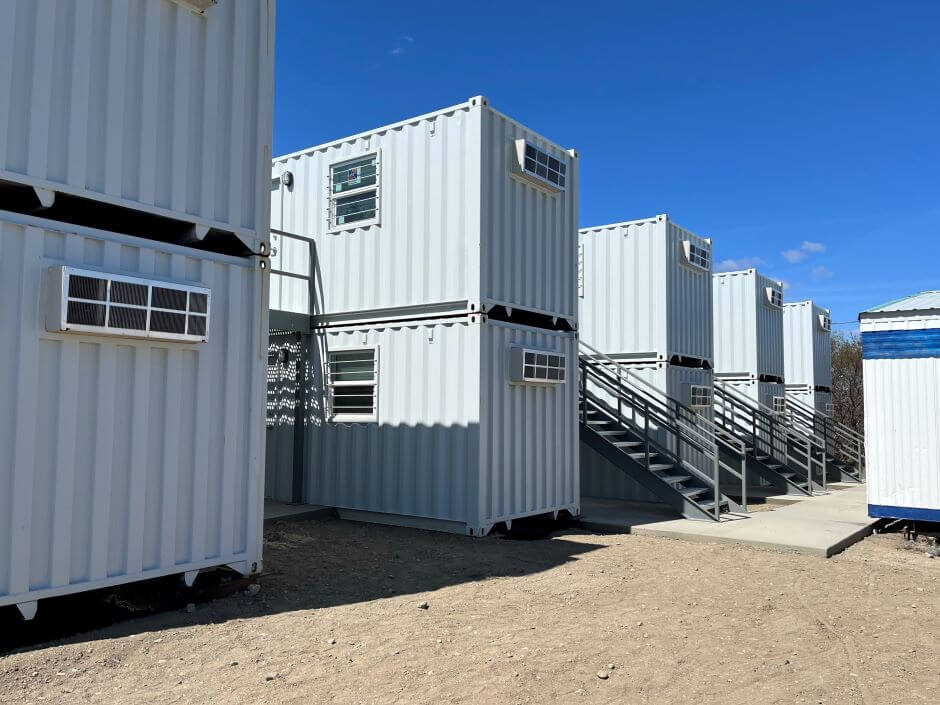
5 Reasons To Choose Modified Shipping Containers for Temporary Workforce Housing
Becca Hubert | Nov 1, 2023 | 3 min read
READ MORE
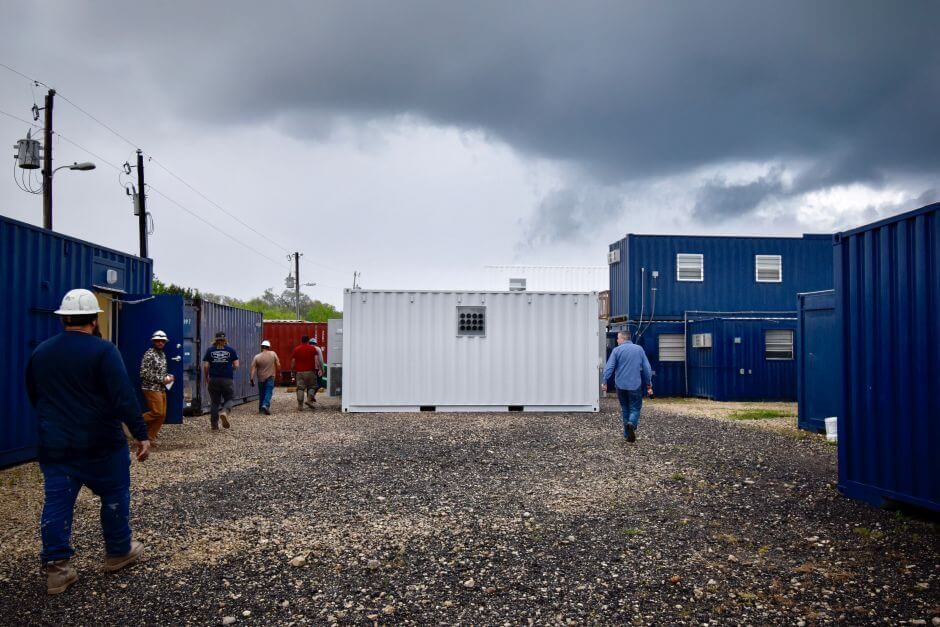
Protecting Field Workers with Climate-Resilient Container Structures
Becca Hubert | Jun 4, 2025 | 4 min read
READ MORE