Modular Construction Savings: How You'll Benefit
Becca Hubert | Nov 15, 2023
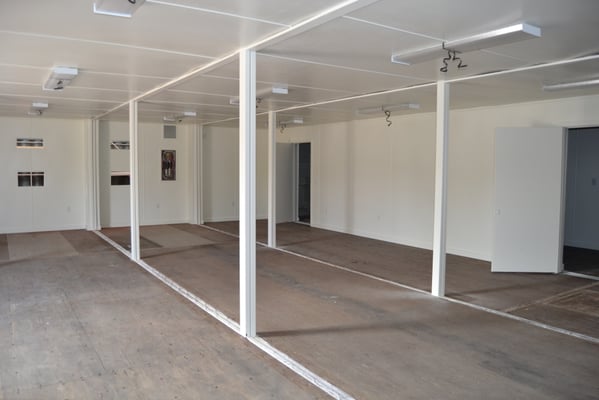
Many building professionals aim to improve their building processes to combat common issues in construction – often related to late projects and expensive cost overruns. Modular construction, a small but growing segment of the $10 trillion global construction market, continues to rise in popularity as a viable alternative building practice. But it’s important to ask: Why modular construction? To answer this question, we must dive into the time and cost saving advantages.
Modular Construction Defined
First, let’s define modular construction to get a clear picture of the building method. The Modular Building Institute defines modular construction as “a process in which a building is constructed off-site, under controlled plant conditions, using the same materials and designing to the same codes and standards as conventionally built facilities – but in about half the time.”
The MBI goes on to clarify that “buildings are produced in ‘modules’ that when put together on-site, reflect the identical design intent and specifications of the most sophisticated site-built facility – without compromise.”
Why Choose Modular Construction?
There are many benefits to modular construction, which you can read more about here. But the two biggest reasons to turn to modular construction boil down to shorter project timelines and cost savings.
Time Savings
Reports show modular projects have a solid track record of accelerating timelines by 20-50% compared to traditional construction. Modular construction teams save time by working on site prep and the offsite manufacturing of building materials simultaneously. The controlled environment is rarely affected by weather delays like a traditional construction site would be. Modular construction manufacturing also has the benefit of standardized processes for consistent, higher quality production.
Cost Savings
Cost savings relate to time savings. When project timelines get cut, so will the cost of the project. Significant time savings from modular construction lead many organizations to improve productivity and efficiency – ultimately leading to faster returns on investment.
According to a 2020 report, 91% of general contractors reported modular construction as having a favorable impact on project budget performance. 48% indicated that costs decreased by more than 10%. Ultimately, this cost savings comes down to the use of readily available materials in manufacturing settings, reduced labor costs thanks to time saved, and the minimization of additional fees as the project progresses, thanks to well-defined upfront project plans.
The Role of Modified Shipping Containers
Modular construction is the combination of smaller modules that are placed together to form larger structures. These modules include frames, beams, and wall panels, but also larger, three-dimensional enclosed units referred to as volumetric construction – including modified shipping containers.
When you turn to this construction method instead of going the traditional route, your projects can remain on schedule and cost effective. In addition to the time and expense-saving benefits, your project is less susceptible to expensive delays, labor shortages, and other obstacles that may be seen in the traditional construction industry.
Falcon Structures is a leading manufacturer of modified shipping container structures with 20 years of experience. Our expert engineers and skilled technicians work hard to exceed high standards and customer expectations, creating remarkable structures using significantly less construction time so you can focus on overseeing the rest of your project.
Want to learn more about the cost savings of modular construction with shipping containers? Reach out to our team at 512-131-1010 or email us at Sales@FalconStructures.com.
SUBSCRIBE
- Shipping Container Modifications
- How-Tos
- Workspace
- Commercial Construction
- Multi-Container Buildings
- Storage Solutions
- Industrial Enclosures
- Oil & Gas
- Bathrooms & Locker Rooms
- Climate Control
- Green Building
- Living Space
- Industry Insight
- Military & Training Facilities
- Water Treatment Solutions
- Energy
THINK INSIDE THE BOX®
WITH OUR BLOG
Get everything from shipping container basics, to detailed how-tos and industry news in our weekly blog. Stay inspired and subscribe!
RELATED BLOGS
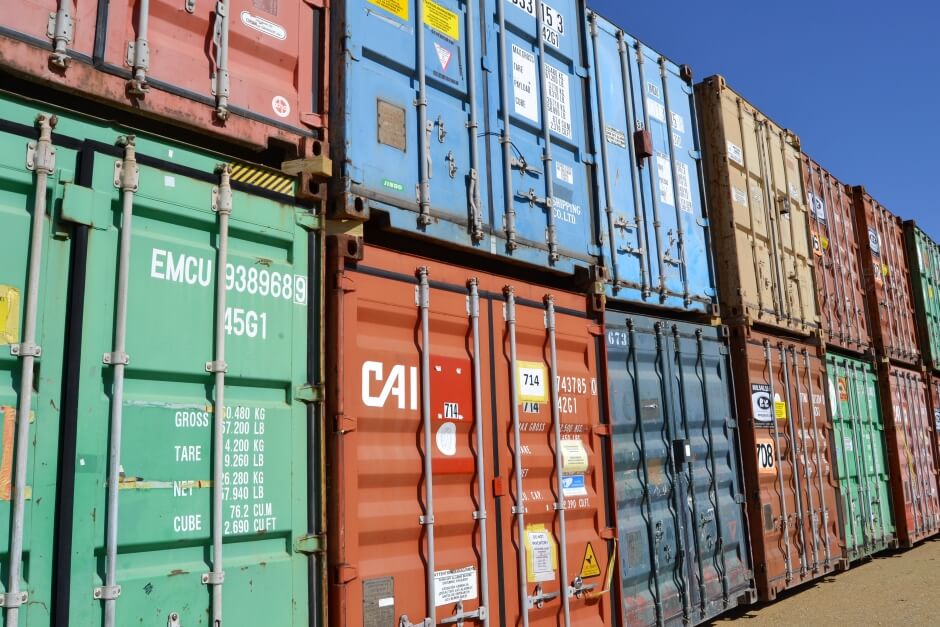
Could Shipping Containers Be a Solution to Affordable Teacher Housing?
Marissa Morin | Apr 19, 2023 | 3 min read
READ MORE
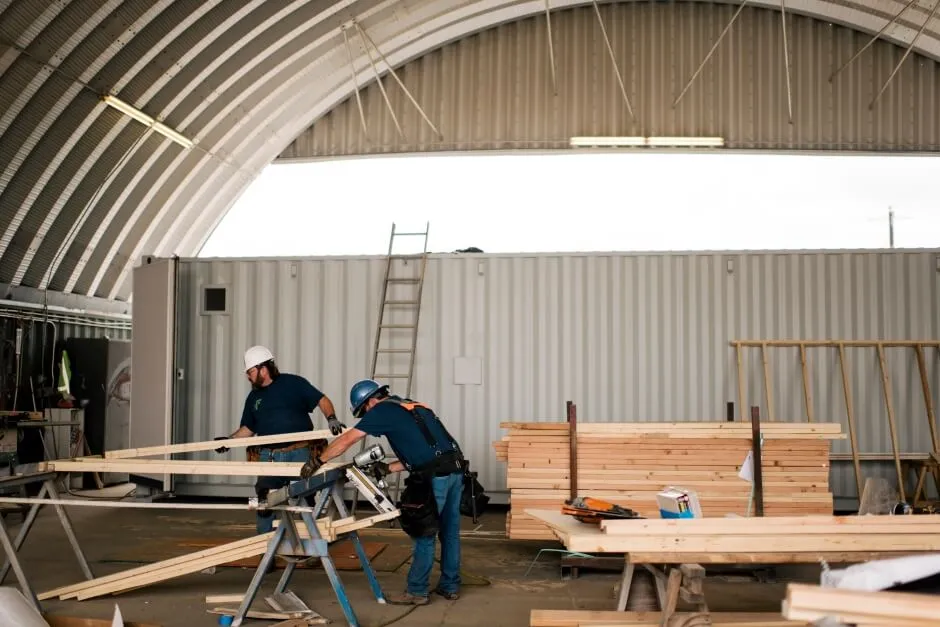
3 Interesting Facts About the Modular Building Industry
Marissa Morin | May 5, 2021 | 3 min read
READ MORE
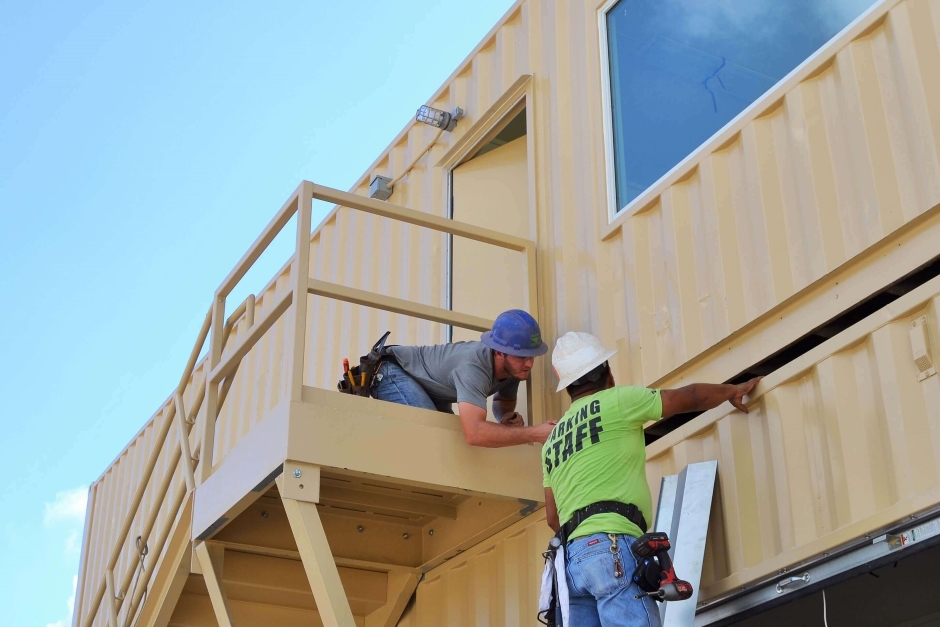
What Is Offsite Shipping Container Construction & Why Is It Important?
Marissa Morin | Apr 20, 2022 | 2 min read
READ MORE