5 Common Modular Building Design Mistakes & Why to Work with an Expert
Marissa Morin | Feb 2, 2022
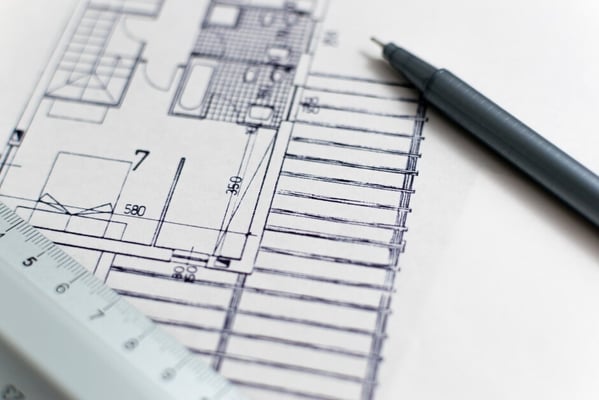
Modular construction is gaining steam and helping speed up construction schedules across the country, but like any new technology, there’s sometimes a learning curve. For contractors and developers, there are a few recurring modular building design mistakes. Fortunately, you can avoid these challenges with better planning, education, and by working with experts in the field.
Skip to:
A brief overview of modular building
Modular construction is the practice of building portions of a structure in an off-site facility and then assembling them as modules in a larger structure. You can think of the modules as LegoTM bricks stacked into a larger structure by crane. Modular building is ideal for buildings with repeating units. For example, Marriot uses modular construction to quickly assemble hotels with repeated rooms.
As opposed to building on-site from the foundation up, modular building keeps most of the building process in a controlled plant environment. When implemented correctly, a manufacturing approach to construction can improve quality control, create a precise construction schedule, and dramatically shorten the time to completion. The market share of modular construction has been steadily growing over the past decade. According to McKinsey & Company, modular construction designs tend to accelerate project timelines by 20-50%.
Modular building design challenges:
1. Change orders present a bigger challenge
It’s not uncommon in traditional construction to slightly pivot designs during the build-out or to plan on a rectification period to correct errors. However, with modular construction, there is much less room for improvisation. As soon as the modules go into production, changing the building’s final design may be very difficult or virtually impossible because changes may impact how the modules fit together. Instead, plan for a longer, more collaborative design phase.
Why work with an expert:
Your team should understand the finality of the building’s design. You can prevent change orders by encouraging collaboration between the architect, the module manufacturer, and the local code official before any modules go into production.
The design phase in modular construction may last longer, but it also dramatically shortens the manufacturing and assembly phase. A thoroughly vetted design will also create a much more reliable project timeline and budget.
2. Some local building officials are unfamiliar with modular building
Usually, local building officials send inspectors to construction sites multiple times to check each phase of the build-out. They may be uncertain of how to assess the safety of a building if a fully finished-out module arrives on the back of a truck. Instead, communicate with the authority having jurisdiction before you build.
Why work with an expert:
The solution varies with the building site’s locality. Some states have created manufactured building programs and have taken steps to familiarize building officials with off-site construction. Other jurisdictions offer no guidance to building officials, pushing them to make one-off decisions about modular structures.
Do research about any existing modular building programs and contact building officials during the design phase. Being prepared with engineer-approved designs can help your case. If the module manufacturer is relatively local, the building official may choose to inspect the factory’s process. In our experience, building officials just want to keep people safe. They will work with you if you loop them in early and transparently.
As modular building structures grow in popularity, we anticipate the permitting process will continue to get easier. In fact, popular demand lead the International Code Council (ICC) to create AC462, an acceptance criterion for assessing the safety of shipping container-based modules. Code officials can now trust that manufacturers with an ICC evaluation service report are producing container modules fit for use as building materials.
3. Crossing multiple state boundaries with oversize loads means a lot of permitting fees
In a case study from the report “Permanent Modular Construction,” a developer lamented that transporting their modules from the manufacturing facility to the job site was a major added cost in part because of permitting oversize loads. Their modules were wide enough to require oversize load permits from each of the six states they crossed. Hiring a lead driver and purchasing six permits for each of their modules drove up their budget.
Why work with an expert:
We recommend hiring a local manufacturer to design modules that fit within trucking limits. One advantage of choosing shipping container-based modules is that they fit onto a truck bed. If modifications do not add to their width or height, container modules will not need oversize permits for transport.
4. Storing the modules before assembly can be expensive
The non-profit Concern for Independent Living built a modular apartment in New York City with the aim of creating affordable housing. Unfortunately, they ran into unexpected costs when the modules arrived before they could get oversize load permits from the city. Because of the delay, the non-profit had the unenviable task of finding storage for an entire apartment building on short notice.
Although they eventually assembled the structure in an impressive twelve days, storing the modules as they waited on permitting was a significant and unexpected expense.
Why work with an expert:
The best solution is to avoid this scenario entirely. As discussed before, communicate with building officials before manufacturing. Determine what transportation permits you’ll need and find out how many modules you can store in your staging area. If you are limited on space, you may want the manufacturer to send out the modules in stages instead of all at once. Ideally, a manageable number of modules would arrive each day, and a crane would stack them as they arrive.
5. Liability can be unclear
Liability is a challenge for any project involving multiple players and pieces. For instance, if a module is damaged during transportation, who is liable? The module manufacturer? The trucking service? The building owner? It’s best to draw up the terms and conditions before manufacturing.
Why work with an expert:
Spell out who is responsible for damage during transportation and other defects in an insurance-backed product guarantee. Just like everyone else on your building team, get your lawyers in early to go over terms and conditions.
The Upsides of Modular Building Design
You may have noticed a recurring theme in our solutions. Success with modular construction means putting a significant amount of thought and planning into the design phase. Regardless, evidence points to significant pay-offs in the overall project timeline if modular construction is properly implemented.
Modular construction designs allow teams to complete projects in significantly less time than traditional construction, thanks to the controlled environment of the offsite facility. Offsite production teams create a consistent quality of work by using materials more efficiently. Modular construction costs are often more predictable, allowing companies to remain within budget.
If you’d like to learn more about modular, offsite construction, check out our downloadable eBook. If you’d like to learn more about the role of modified shipping containers in modular building, check out what a modified shipping container expert wants you to know.
SUBSCRIBE
- Shipping Container Modifications
- How-Tos
- Workspace
- Commercial Construction
- Multi-Container Buildings
- Storage Solutions
- Industrial Enclosures
- Oil & Gas
- Bathrooms & Locker Rooms
- Climate Control
- Green Building
- Living Space
- Industry Insight
- Military & Training Facilities
- Water Treatment Solutions
- Energy
THINK INSIDE THE BOX®
WITH OUR BLOG
Get everything from shipping container basics, to detailed how-tos and industry news in our weekly blog. Stay inspired and subscribe!
RELATED BLOGS
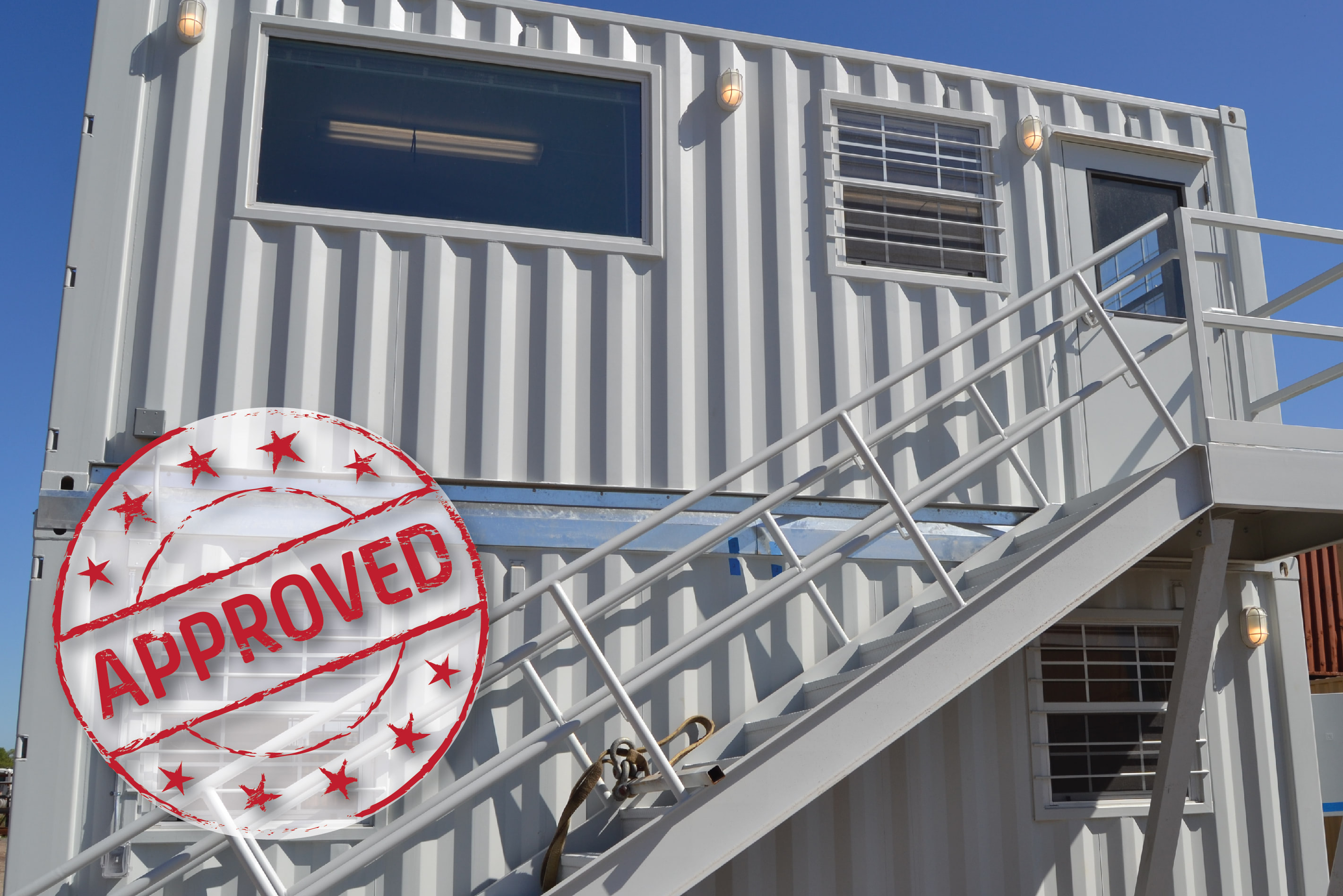
Shipping Containers are Joining Building Code. Now What?
Paige Welsh | Feb 27, 2019 | 2 min read
READ MORE
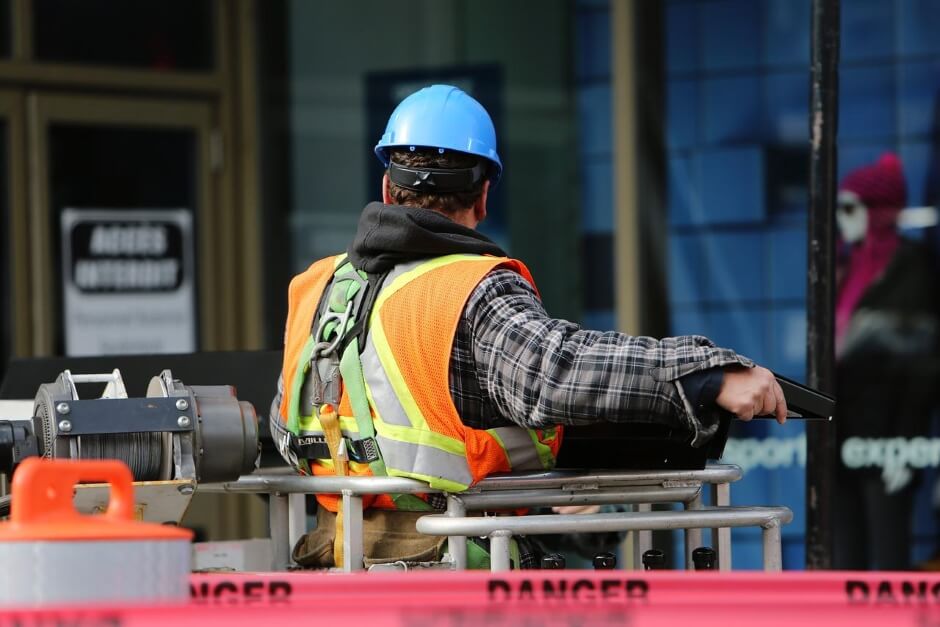
Safety in Construction: Ensuring Your Team is Well Equipped
Marissa Morin | Apr 27, 2022 | 3 min read
READ MORE
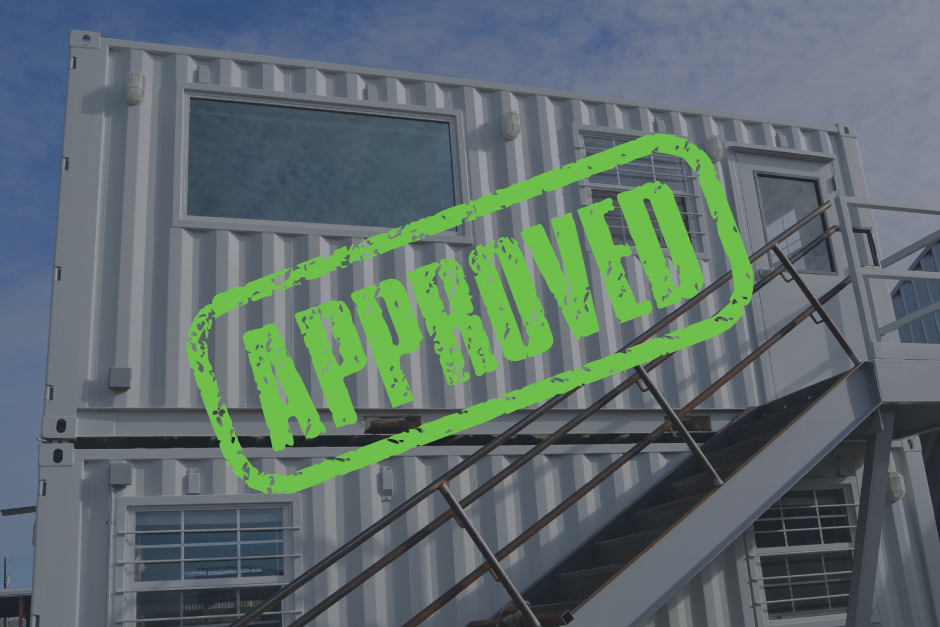
Understanding Permitting: Shipping Container Buildings Code Compliance
Marissa Morin | Sep 28, 2022 | 3 min read
READ MORE